È assai difficile quantificare tutte le attività di ricerca tecnologica nell’industria dello sci. è comunque evidente cone una ricerca mirata solo a questo settore non sia economicamente sostenibile, quindi tutte le evoluzioni strutturali si realizzano attingendo da altri settori industriali che ne favoriscono la crescita. Si è incrementato lo scambio di informazioni e di esperienze acquisite in altri campi del settore sportivo che hanno a disposizione risorse più consistenti da destinare alla ricerca.
Il più significativo sviluppo nella produzione dello sci è avvenuto negli anni cinquanta quando si è passati da una lavorazione artigianale a un processo industriale. Sono stati impiegati materiali più resistenti e di maggior durata come l’ergal che chiudeva a sandwich l’anima di legno. La crescita è avvenuta in modo graduale e ha portato alla realizzazione di attrezzi più performanti.
L’’introduzione sul mercato dei materiali fibrosi come la fibra di vetro ha aperto un nuovo orizzonte di sperimentazione anche nella produzione dello sci. L’importante era capire come queste fibre potessero essere impiegate per sfruttare al meglio le loro proprietà. La conoscenza poi dei materiali compositi che sono la combinazione di più elementi ha maggiormente mutato e perfezionato la costruzione di questi attrezzi che sono cambiati anche nella loro estetica. (Vedi foto qui sotto)
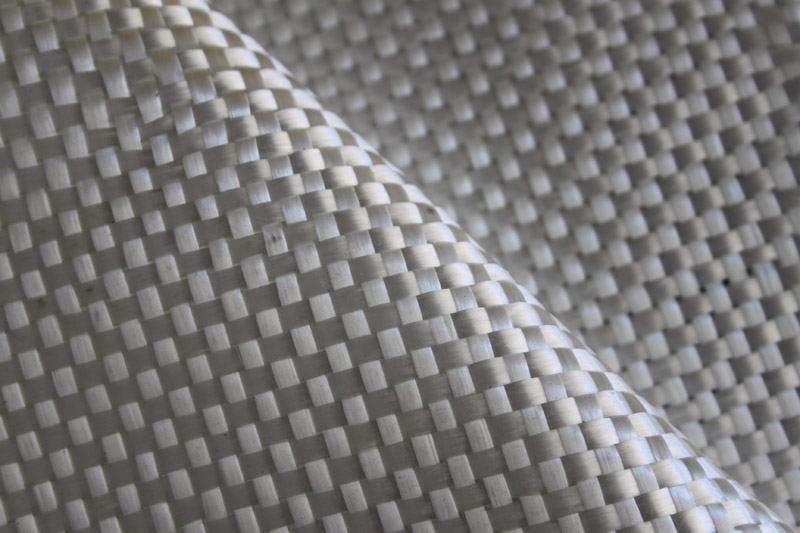
In questi ultimi decenni la ricerca multidisciplinare ha messo a punto nuovi materiali avanzati sia polimerici che fibrosi ad alto contenuto tecnologico che danno la possibilità di sostituire la fibra di vetro nei compositi con le nuove fibre di carbonio, kevlar e ceramiche. (Vedi foto qui sotto)
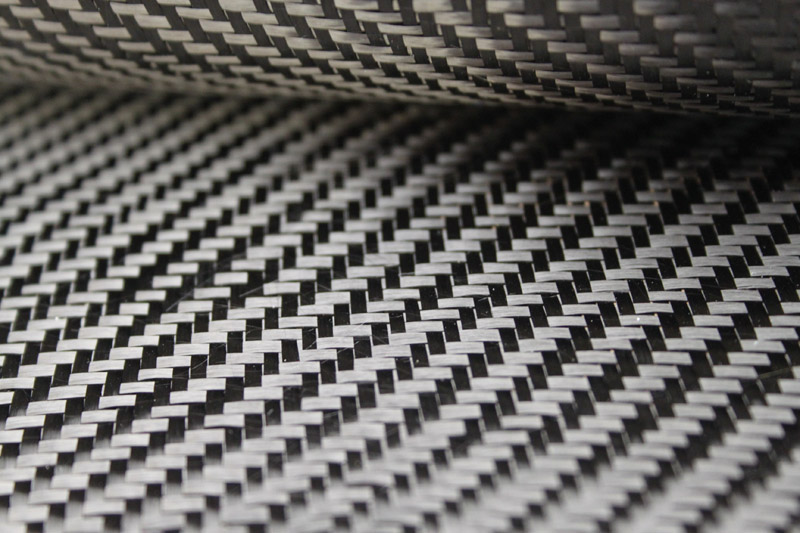
Le fibre di carbonio sono nate per risolvere i problemi di peso, rigidità e resistenza sia nell’industria aerospaziale che in quella automobilistica. Il primo processo produttivo di queste fibre è stato effettuato negli Stati Uniti utilizzando fibre rigenerate di rayon ed è stato poi perfezionato in Inghilterra e Giappone utilizzando fibre tessili acriliche modificate.
I processi produttivi hanno in seguito visto l’impiego di poliacrilonitrile (PAN) per la realizzazione delle fibre di carbonio attraverso il processo di trafilatura e i successivi processi di carbonizzazione in atmosfera inerte e grafitizzazione che danno alla fibra una maggior purezza. Le fibre ad alto modulo si ottengono a 2800°C, mentre a temperature inferiori si ottengono fibre a modulo intermedio.
Queste fibre hanno importanti proprietà meccaniche, elevata resistenza, ottima rigidità, alto modulo elastico ed elevata conduttività elettrica. Il loro peso è molto contenuto, un decimetro cubo pesa soltanto kg 1,6.
Un primo modello di sci che ha sfruttato le potenzialità del carbonio è stato l’HTS – High Tech Ski – prodotto con una tecnologia avanzata in autoclave sotto vuoto. I tessuti pre-impregnati, avvolti attorno ad un’anima di nido d’ape nomex pre-assemblata formavano una scatola armonica antitorsionale e venivano posizionati in particolari stampi studiati appositamente per il sistema sotto vuoto. La polimerizzazione dello sci avveniva in autoclave per consolidare in modo ottimale le stratificazioni delle fibre pre-preg. La superficie dell’attrezzo rimaneva in carbonio a vista (Vedi foto qui sotto)

Il fascino e l’opportunità di utilizzare le fibre di carbonio per la costruzione di svariati attrezzi sportivi avevano indotto diverse aziende ad investire tempo e risorse nello studio e nella ricerca di queste fibre innovative.
Oggi con i sistemi computerizzati e la modellazione FEM (Finite Element Method- Modelli Elementi Finiti) è possibile progettare l’impiego del carbonio a partire dall’organizzazione tessile. Una singola fibra ha scarso valore strutturale quindi le fibre devono essere tessute con determinate geometrie e coesionate da una matrice resinosa per ottimizzarne le sinergie. La forma tessile più semplice è quella tradizionale composta da ordito e trama. La lavorazione avviene con telai automatici che, tramite programmi predeterminati, dispongono alternativamente i fili di ordito con quelli di trama per originare un intreccio ortogonale. L’evoluzione delle tecnologie in campo tessile ha portato alla realizzazione di rinforzi fibrosi multi assiali a maglia in catena (Vedi foto qui sotto)
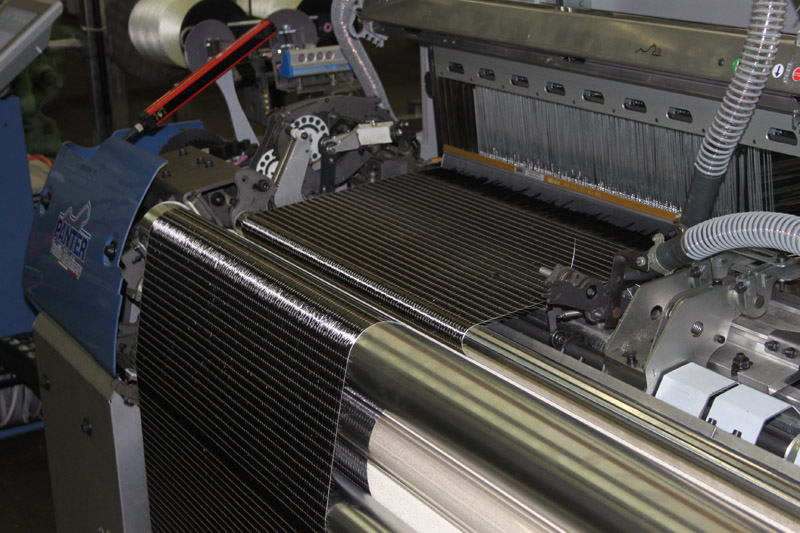
Le fibre lunghe di carbonio possono essere unite in matasse di 12.000 o più fili chiamate roving che, assemblate in modo parallelo, formano un tessuto monodirezionale.
La tessitura può avvenire anche in forma ibrida quando le fibre di carbonio sono unite con fibre di kevlar che hanno una notevole resistenza a fatica ed un’ampia capacità di assorbire le vibrazioni (Vedi foto qui sotto)
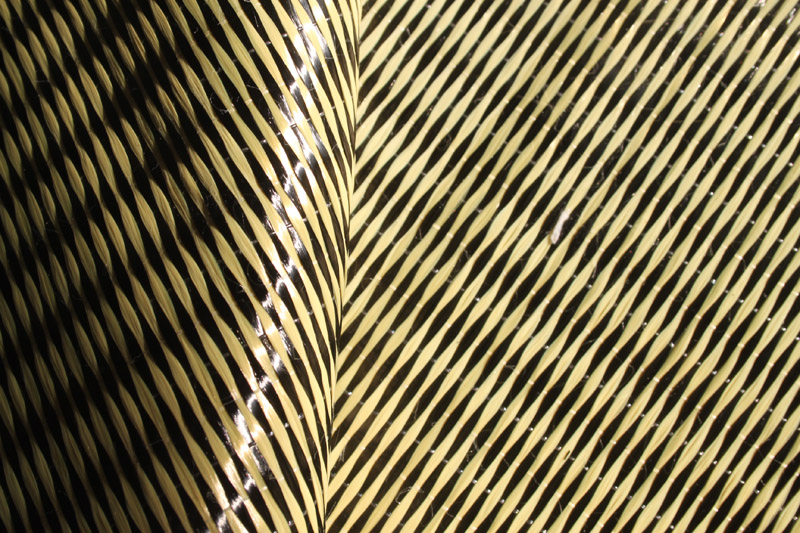
La tecnologia a sandwich, usata in modo particolare per gli sci agonistici, vede l’impiego del carbonio in modo mirato. Un tessuto monodirezionale ibrido formato da carbonio e kevlar viene usato sull’asse di trazione. In questo modo si ottimizzano le caratteristiche meccaniche nel settore in cui lo sci è sottoposto ad elevati sforzi dinamici generati dal terreno non uniforme, dalla velocità e dall’ampiezza dei raggi di curva. La torsionalità di punta e di coda è regolata con insertazioni modulari di carbonio multi assiale. La portanza viene calibrata con multistrati di carbonio a basso spessore che si interfacciano con dei laminati metallici di titanal e delle stratificazioni elastomeriche per regolare la reattività ed abbassare il momento di inerzia.
La massima sinergia si ottiene con l’incollaggio di tutti i materiali con le resine epossidiche che hanno buone caratteristiche elastiche e permettono lo scorrimento interlaminare.
La tecnologia monocap è caratterizzata da una struttura a semi-guscio che vede nei tessuti tecnici di carbonio il materiale ideale per la produzione. Le prestazioni del carbonio usato in questo campo sono state ulteriormente migliorate con innovative soluzioni tessili. Attraverso l’uso di telai elettronici si tessono contemporaneamente ai fili di carbonio dei filati termoplastici che si intersecano tra la trama e l’ordito (Vedi foto qui sotto)
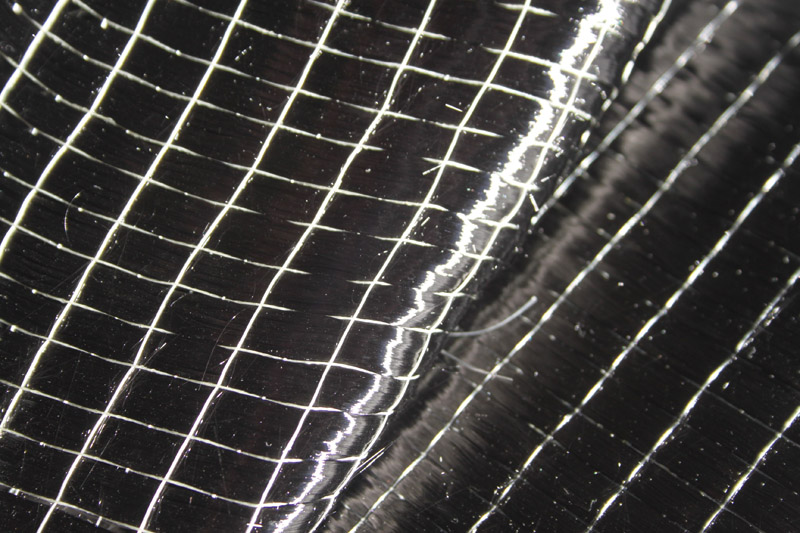
Questi filati appositamente studiati sono a basso punto di fusione (50°C) e sono compatibili con le resine epossidiche. Le fibre così lavorate sono poi dimensionate nei centri di lavoro per essere assemblate in speciali stampi a conchiglia che riproducono la geometria dello sci (Vedi foto qui sotto)
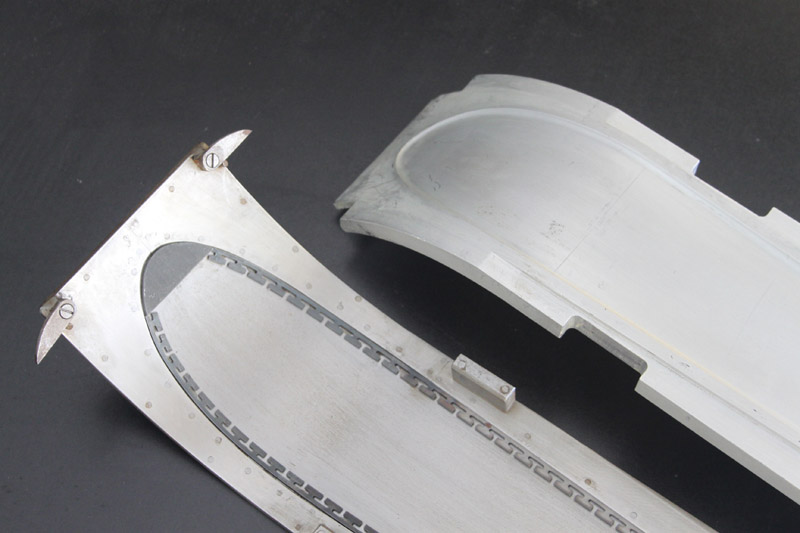
Il calcolo matematico del progetto e le simulazioni software indicano quante stratificazioni di carbonio sono necessarie per l’asse di trazione e la scocca di compressione che avvolge l’anima pre-assemblata.
Le fibre e i materiali che compongono lo sci sono impregnati con resine epossidiche a bassa densità. Il processo di polimerizzazione avviene sotto pressa dove la curva termica progressiva raggiunge i 120°C. La resina allo stato fluido subisce una serie di trasformazioni passando da uno stato gelificato gommoso ad uno stato vetroso. I filati termoplastici si sciolgono al punto di gelificazione e si amalgamano nel reticolo tridimensionale della resina nella fase in cui si formano i legami chimici.
L’ottimizzazione del processo di polimerizzazione è legato al tempo di riscaldamento e al successivo raffreddamento nel ciclo di lavorazione. La fibra di carbonio che subisce questo trattamento assume una fisionomia completamente nuova. La reattività e la rigidità sono in relazione con la percentuale di filato termoplastico sciolto nella resina epossidica che consente una equilibrata ripartizione degli sforzi all’interno della geometria dello sci.
Il modulo elastico del carbonio deve essere correttamente bilanciato per controllare le forze primarie che creano il movimento nello sci monocap, vale a dire la forza di gravità che muove le masse nel sistema, la resistenza a compressione sulla neve e le forze dovute agli spostamenti del peso dello sciatore.
Le prove a fatica hanno evidenziato le notevoli prestazioni degli sci costruiti con questa nuova tecnologia. Per l’effettuazione di queste prove viene applicato un carico di 80 chilogrammi per 100.000 cicli, ad una frequenza di 30 cicli al minuto. Al termine delle prove non si riscontrano anomalie o rotture e si confermano i valori della simulazione computerizzata ottenuta in fase di progetto (Vedi foto qui sotto)
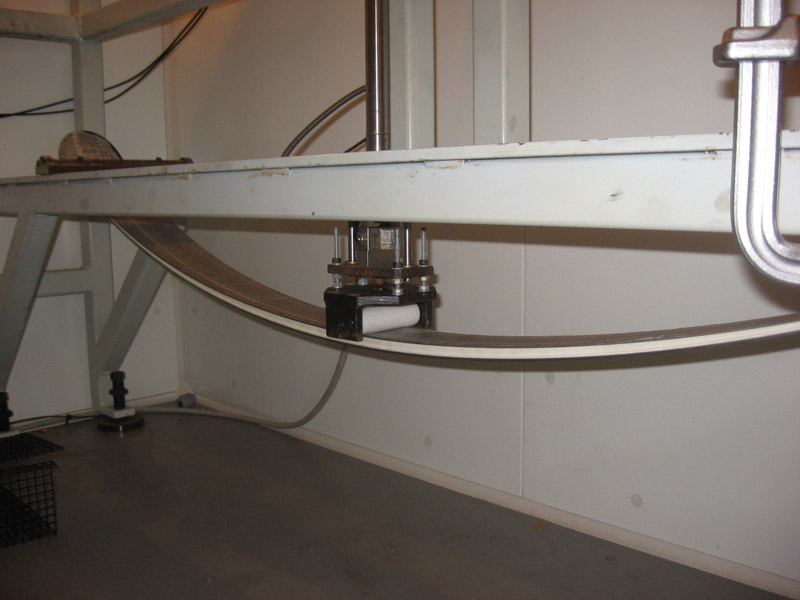
Le fibre di carbonio sono i materiali più studiati nei sistemi compositi avanzati dove si ricercano forme tessili sempre più performanti. Le sinergie che si ottengono unendo le fibre di carbonio con i blend polimerici sono notevoli e sfruttando le caratteristiche di questi materiali si può dare un nuovo impulso alla produzione di attrezzi innovativi.
Add Comment